Adapting Bin Management Feature In NetSuite
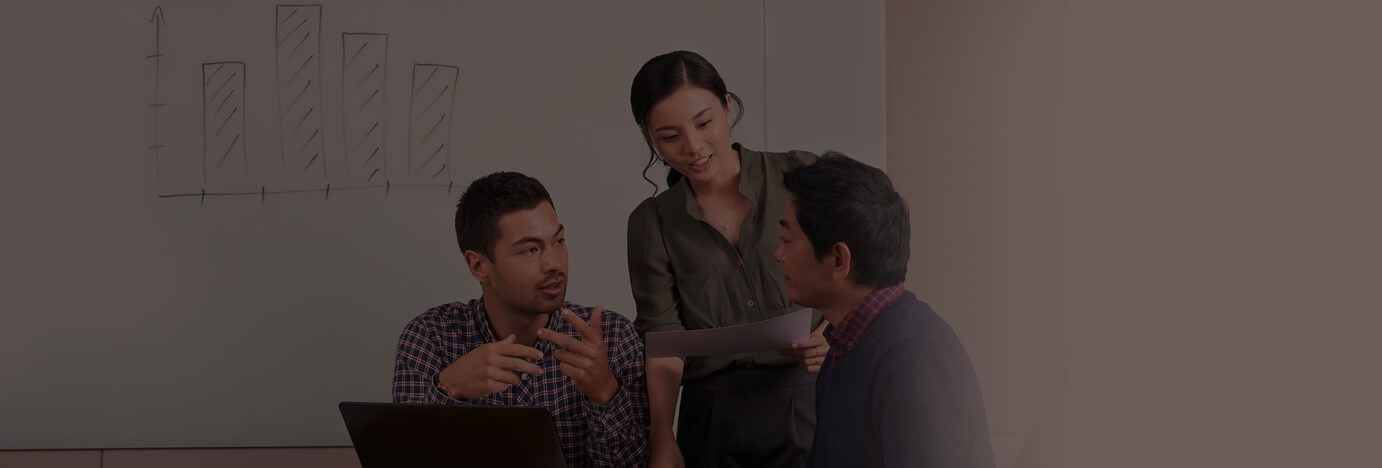
NetSuite Bin Management System improves the inventory management of a warehouse, allowing the inventory to be received into appropriate bins, within the rack system. This helps to track the stock level of a particular item based on the order fulfillment and know what items need to be stocked, and where, after receiving from a vendor.
Major NetSuite Bin Management Features
There are two different types of features for NetSuite Bin Management. They are;
Basic Bin Management
A basic bin management feature assists the user to track and monitor the inventory items located in the warehouse or bins.
In this feature, a user must associate bins with items before retrieving them on transactions.
Users can create bin records to identify specific places within the warehouse and associate the item with each bin on the item record. As a result, the bin to be used when an item is added to the transaction can easily be identified. Hence, a user knows the exact place to stock the item in the warehouse after receiving or to get it to fulfill an order.
This feature has limited functionality. The user can not use lot numbered items or on a per-location basis bin with serial.
Advanced Bin / Numbered Inventory Management
Advanced Bin / Numbered Inventory Management System provides full-fledged features including tracking inventory in bins, adding lot numbered items as well as serial numbered items, on a per-location basis. The Major advanced functions this system offers includes;
1. No Pre-Association Requirements
The user can make use of bins on transactions without being required to pre-associate bins to items is the primary feature of the Advanced Bin / Numbered Inventory Management system. Enabling this system helps you to utilize any bin for any item, even if it is not recognized on the item’s record. Associating bin with any item on the item record displays the Associated bins list on transactions. Thus the user can create a preferred bin for an item.
2. Use Bins For Serialized And Lot Numbered Items
Basic Bin Management has limited features. It limits the choice of associating serial or lot items with bins. Whereas an advanced bin management system permits the user can utilize the bins for lot numbered items as well as for serial numbered items. This is possible when Lot Tracking or Serialized Inventory features are enabled in the Advanced Bin Management System.
3. Use Bins On A Per-Location Basis
Advanced Bin Management System allows us to choose and use bins at only specific locations if the Multi-Location Inventory feature is enabled.
4. Sub-tabs Available
The Advanced Bin / Numbered Inventory Management feature provides the subtabs like Inventory Numbers, Bin Numbers, and Inventory Detail on item records.
Enabling Basic/Advanced Bin Management
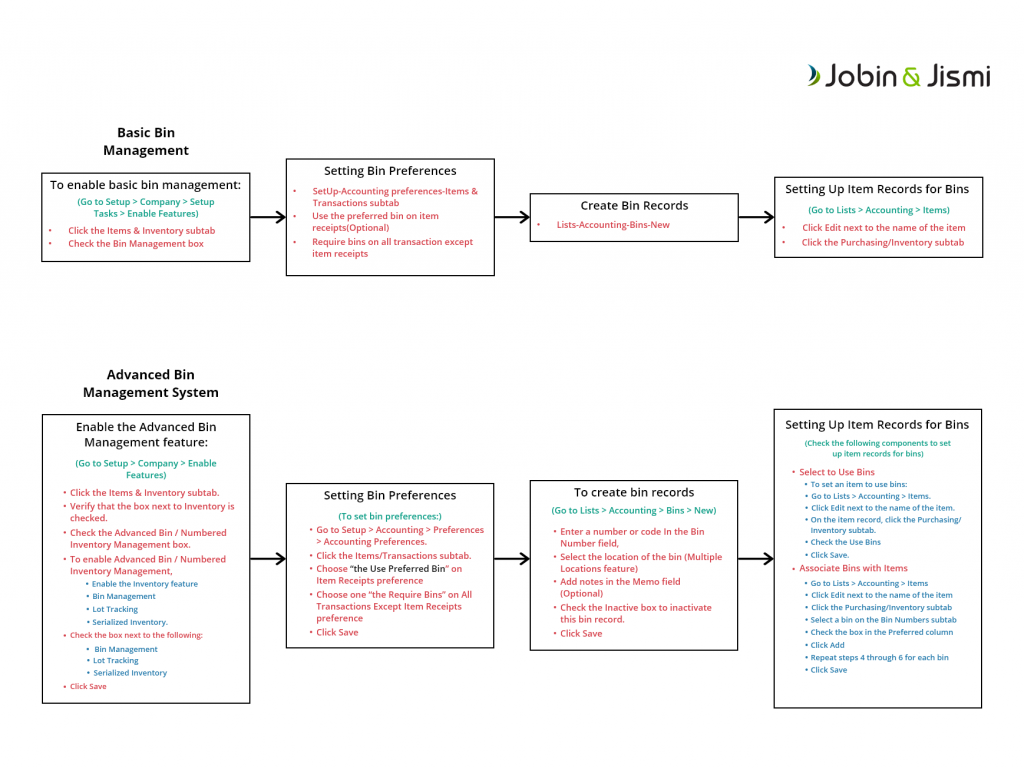
Bin Putaway Worksheet
The putaway worksheet allocates the bin or section in the warehouse. Bin putaway worksheet is used to print the record of bin numbers of the items to be refilled in different sections of the warehouse. The item that uses the bin has more total on-hand count compared to the combined count of the associated bins.
The required list can be uploaded at any time with the date, preferred bin number, items and quantity to put away, and a blank area for notes. Once we receive the item, they are moved to the put away in bins.
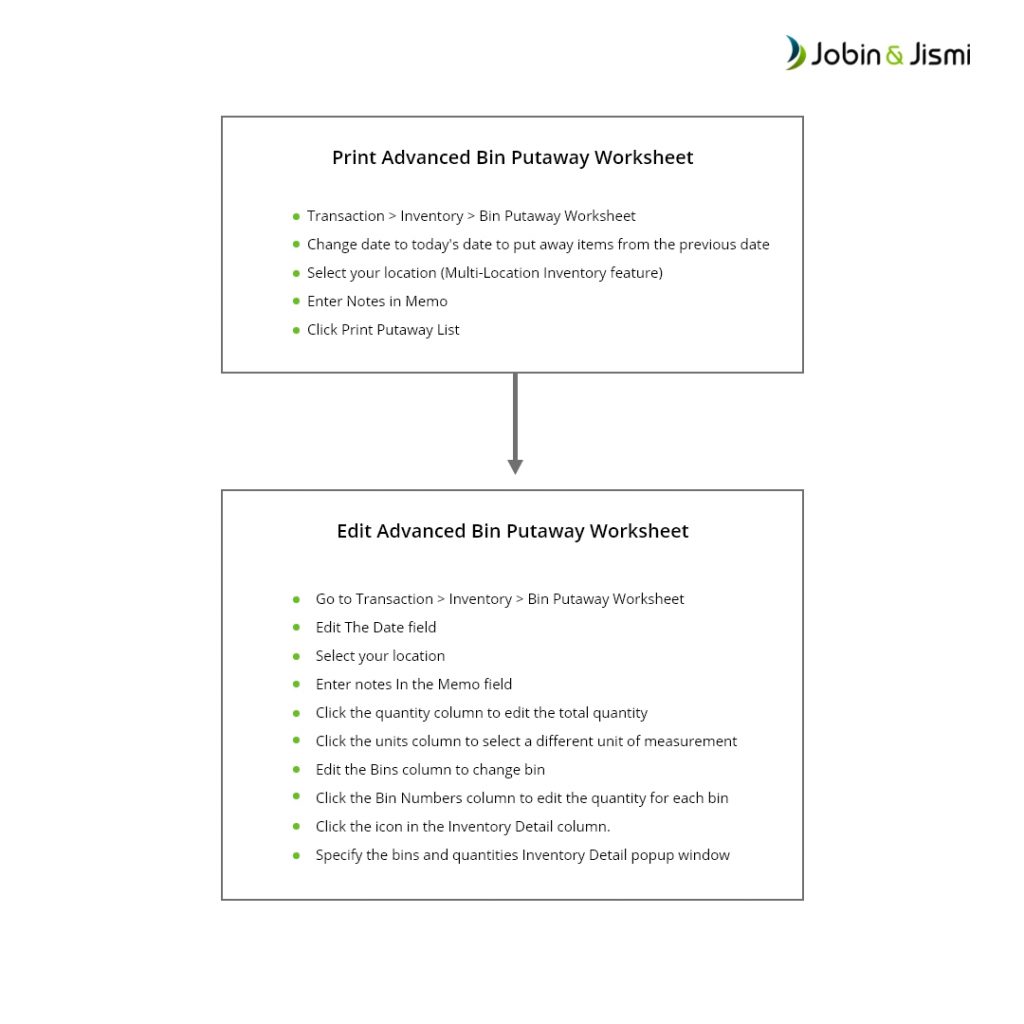
If you are using the Advanced Bin / Numbered Inventory Management feature the following steps are applicable.
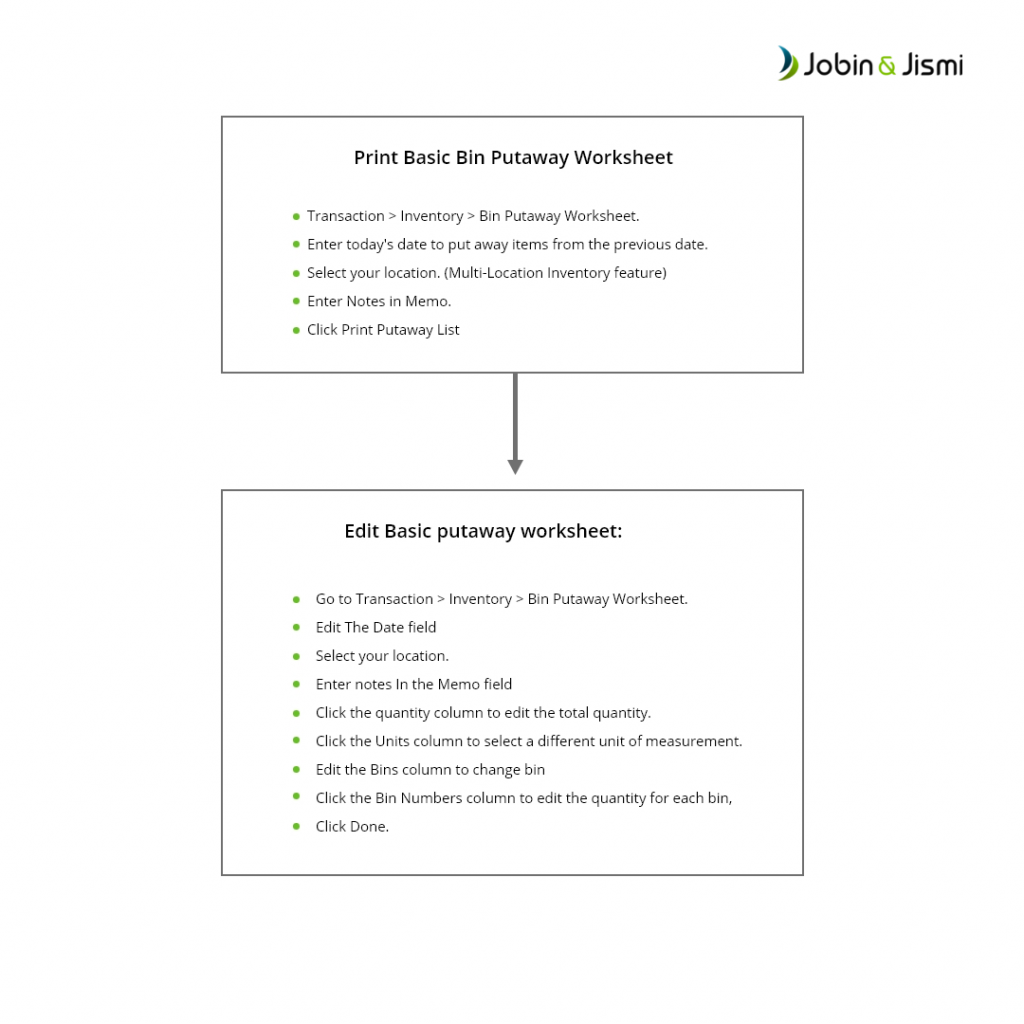
Preferences while Using Bin Management System
The following sections explain the different preferences available while using bins.
Putting Away Items In Bins
To quickly put away the items arranged in a bin change the value of the quantities of the items arranged in each bin. Enabling the Use Preferred Bin on Item Receipts preference helps to maintain all the items in the chosen bin as default. You can put away an item in the bin in the future by changing the volume of the selected bin to zero.
Receiving With Bins
Bin numbers are added to various transactions after submitting a purchase order or receiving a customer return. This is done for the following transactions:
- Cash Refunds
- Vendor Bills
- Inventory Adjustments
- Checks
- Inventory Transfers
Bins On Sales
Bin numbers are added to various transactions after placing a sales order by the customer such as;
- Picking tickets
- Item fulfillments
- Invoices
If required a user can change the items between bins after an item is added to one or more bins.
Bins On Picking Tickets
A user can automatically print the picking ticket to locate the bin of a specific item required to complete the order. In case if a different quantity is pulled from the bin, it is also added to the picking ticket. The user can edit the quantity of a taken item on the order fulfillment page.
Data Per Bin
Both the Basic and advanced features of the bin are not used to calculate an item costing per bin. Only on-hand quantity calculates as per the bin. Items that come under the available, committed, backorders, and ordered quantities are also not tracked per bin.
Specifying Bins On Transactions
Bins play a vital role in carrying out proper transactions with bin items. These include transactions like invoices, all-cash sales, and negative inventory adjustments. It is important to maintain bins even after enabling preference, the Require Bins on All Transactions Except Item Receipts.
Bins And Assembly Items
Assigning a bin is essential for any component item that uses the bin when the user accesses the Assembly Items feature. When a parent assembly item uses bins, the user must allocate a bin to unbuild the parent assembly item. One can not allocate a bin for a member item in an unbuilt or for an assembly item unless the Require Bins on All Transactions except Item Receipt preference is enabled.
Inventory Detail Sub-record
The user can utilize the popup selector for choosing a bin for an item. A user can filter the bin through some easy steps. The user must choose a bin, then enter the desired quantity and select the Inventory Detail button. The inventory detail button is shown in the records and transactions.
NetSuite Bin Management system facilitates the best inventory management in a warehouse by facilitating real-time visibility to the records of the inventory stored. This item is very handy, especially if the inventories are stored in more than one physical location. The exceptional features of NetSuite Bin Management System like the ability of real-time bin counting, managing Picking strategies, Bin replenishment, FIFO and FEFO control, etc, improves the inventory and picking accuracy and warehouse performance.
on LinkedIn